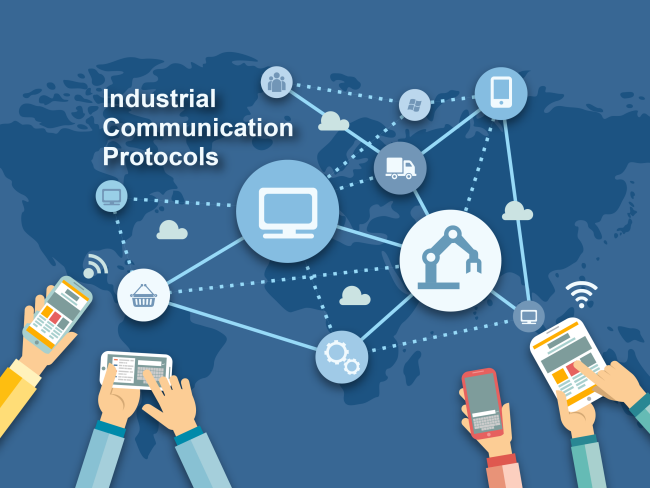
บทความ | ธงชัย ธงวิจิตรมณี
ทีมระบบไซเบอร์-กายภาพ (CPS)
หน่วยทรัพยากรด้านการคำนวณและไซเบอร์-กายภาพ (NCCPI)
ภาพประกอบ | กรรวี แก้วมูล
ระบบอัตโนมัติอุตสาหกรรม (Industrial Automation Systems) ทำหน้าที่เชื่อมโยงอุปกรณ์ต่าง ๆ ประกอบด้วย เครื่องกล อิเล็กทรอนิกส์ เซนเซอร์ ตัวขับเร้า (actuator) และคอมพิวเตอร์ที่ถูกออกแบบเพื่อลดหรือหลีกเลี่ยงการสั่งงานจากมนุษย์ และสามารถทำงานได้หลากหลายตามที่ต้องการได้ เพื่อให้เกิดประโยชน์ในด้านการลดค่าใช้จ่าย มีคุณภาพเพิ่มขึ้น และมีประสิทธิภาพโดยรวมมากขึ้น ตลอดจนมีความปลอดภัยในการทำงาน [1,2] การสื่อสารในอุตสาหกรรม (Industrial Communication) เป็นระบบสื่อสารระหว่างอุปกรณ์ต่าง ๆ ในระบบอัตโนมัติอุตสาหกรรม และมีส่วนสำคัญมากในการพัฒนาระบบอัตโนมัติอุตสาหกรรมให้มีความทันสมัย รายงานนี้เป็นการศึกษาการสื่อสารในอุตสาหกรรม Industrial Communications ที่มีโพรโทคอลหลักที่ใช้แพร่หลาย เช่น PROFINET, PROFIBUS, EtherCAT, EtherNet/IP, Modbus RTU, Modbus TCP เป็นต้น
การพัฒนาการสื่อสารในอุตสาหกรรม
ระบบสื่อสารในอุตสาหกรรมได้ผ่านการพัฒนาอย่างต่อเนื่องตั้งแต่เริ่มแรกในปีคริสต์ทศวรรษ 1980 [3,4] จนถึงปัจจุบัน โดยอาจแบ่งการพัฒนาที่สำคัญออกเป็น 3 ช่วง ได้แก่ 1. Classical Fieldbus system 2. Industrial Ethernet และ 3. Wireless networks in automation โดยรายงานฉบับนี้จะกล่าวถึงเฉพาะสองลำดับแรกเท่านั้น
1) Classical Fieldbus System
การสื่อสารในอุตสาหกรรมในยุคเริ่มแรกจะใช้คำว่า Fieldbus system โดยคำนี้ถือกำเนิดจากกระบวนการในโรงงานเคมีและได้ถูกใช้มาจนถึงปัจจุบัน และนิยามของคำนี้จาก International Electrotechnical Commission (IEC) 61158 ระบุว่า “A fieldbus is a digital, serial, multidrop, data bus for communication with industrial control and instrumentation devices such as-but not limited to-transducers, actuators and local controllers.” และ Fieldbus ถูกสร้างขึ้นมาเพื่อทดแทนการเชื่อมต่อสายสัญญาณแบบ Star ซึ่งเป็นการเชื่อมสายสัญญาณจุดต่อจุดระหว่างขาเข้าและขาออกของอุปกรณ์ดิจิทัลหรืออนาล็อกกับอุปกรณ์ควบคุมศูนย์กลาง โดยเชื่อมต่อสายสัญญาณเป็นแบบ Line หรือ Bus ด้วยสายสัญญาณเส้นเดียวและมีขั้วต่อปลายทางแบบ DB 9 pins โดยมีอินเตอร์เฟซแบบ RS232 หรือ RS485 ระบบการสื่อสารแบบ Fieldbus ถูกให้ความสำคัญจากแนวคิดเรื่อง Automation Pyramid ซึ่งมีรายละเอียดใน The International Society of Automation (ISA) ในมาตรฐานเลขที่ 95 หรือ ISA-95 [5]
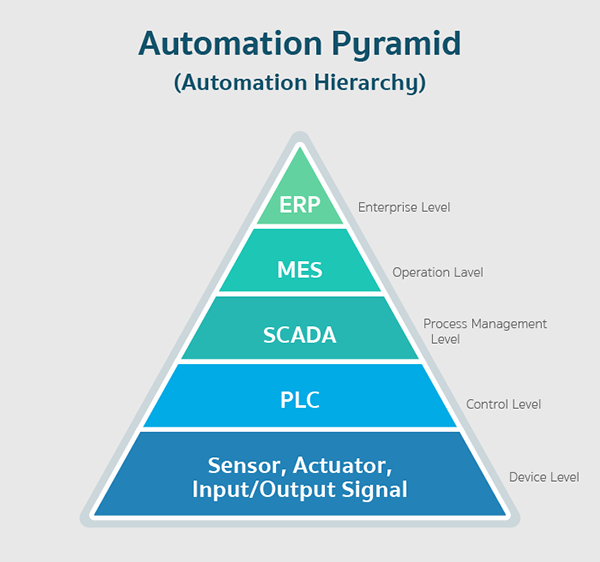
มาตรฐาน ISA-95 พัฒนาต่อยอดจาก Purdue Reference Model for Computer-integrated Manufacturing (CIM) ซึ่งได้สร้างแนวคิดในช่วงคริสต์ทศวรรษ 1970 ในยุคที่อุปกรณ์ทางอิเล็กทรอนิกส์และคอมพิวเตอร์เพิ่งพัฒนาในยุคแรก และใน ISA-95 Part 1: Models and Terminology ได้กล่าวถึง Automation pyramid ดังแสดงในรูปที่ 1 ประกอบด้วย 5 ชั้น ตามลำดับดังนี้
เริ่มจากชั้นบนสุดคือชั้นที่ 4 บทบาทหรือหน้าที่ทางธุรกิจ ได้แก่ Enterprise Resource Planning (ERP), Material Requirement Planning (MRP), และ Supply Chain Management (SCM) เป็นต้น
ชั้นที่ 3 การจัดการควบคุมการผลิต ประกอบด้วยชั้นที่ 3 ลงไปจนถึงชั้นที่ 0 โดยชั้นที่ 3 ประกอบด้วย Manufacturing Execution System (MES), Laboratory Information Management System (LIMS), Quality Management (QM) เป็นต้น ชั้นที่2 ประกอบด้วย Supervisory Control And Data Acquisition (SCADA) ชั้นที่ 1 ประกอบด้วย Distributed Control System (DCS), Open Control System (OCS), และ Programmable Logic Controller (PLC) ที่ใช้เชื่อมต่อกับ ชั้นที่ 0 ประกอบด้วย sensors และ ตัวขับเร้า เป็นต้น ซึ่งเป็นกระบวนการทางฟิสิกส์และเคมีที่ระบบต้องการควบคุม โดยการเชื่อมต่อของการจัดการควบคุมการผลิตจะใช้เทคโนโลยี Fieldbus เชื่อมต่อแบบ serial ชนิด RS232 ที่เป็นการเชื่อมต่อจุดต่อจุดในช่วงแรก และ ต่อมาเป็นชนิด RS485 ซึ่งเชื่อมต่อแบบ bus network ที่มีความสามารถแบบ multi-dropper และ multi-point [4] และทำให้ความสามารถในการเชื่อมต่ออุปกรณ์ต่าง ๆ มีจำนวนมากสุดเท่ากับ 32 ชิ้น รวมถึงมีความยาวสายสัญญาณสูงสุดเท่ากับ 1,200 เมตร และมีความเร็วส่งผ่านข้อมูลสูงสุดเท่ากับ 10 Mbit/s ในยุคแรก และต่อมาอาศัยเทคโนโลยี Industrial Ethernet ทำให้มีความเร็วส่งผ่านข้อมูลสูงสุดเท่ากับ 10/100 Mbit/s ในยุคต่อมา
ในพัฒนาการของระบบ Fieldbus จะเห็นได้ว่า โพรโทคอลคือข้อกำหนดที่ใช้เพื่อเป็นมาตรฐานสำหรับการสื่อสารระหว่างคอมพิวเตอร์ หรือภาษาที่ใช้สื่อสารระหว่างคอมพิวเตอร์บนเครือข่าย จะมีความหลากหลายเพิ่มขึ้นอย่างมากในช่วงคริสต์ทศวรรษ 1980 อันเกิดจากพัฒนาการของฮาร์ดแวร์ด้าน Microprocessors การพัฒนาของวิศวกรรมด้านการส่งผ่านข้อมูลในสายโทรศัพท์ และที่สำคัญการพัฒนาของวิศวกรรมคอมพิวเตอร์ที่ได้เสนอรูปแบบมาตรฐาน The International Organization for Standardization (ISO) เกี่ยวกับ Open System Interconnection (OSI) ในช่วงต้นปี ค.ศ 1980 เพื่อเป็นมาตรฐานกลางอ้างอิงการสื่อสารและเปรียบเทียบการทำงานบนเครือข่าย หลังจากนั้น โพรโทคอลเกี่ยวกับ Fieldbus ได้เกิดขึ้นมากมายนับจากนั้น เพราะระบบอัตโนมัติได้ถูกใช้แก้ปัญหาในหลากหลายอุตสาหกรรมไม่เพียงแต่ในโรงงานการผลิต ยังใช้ในระบบการควบคุมอาคารและบ้านเรือน ระบบควบคุมในรถยนต์ ระบบควบคุมในอากาศยาน ระบบควบคุมไฟฟ้ากำลัง และ ระบบควบคุมเครื่องจักรในอุตสาหกรรมผลิตเซมิคอนดักเตอร์ เป็นต้น ซึ่งการประยุกต์ใช้แก้ปัญหาในหลากหลายอุตสาหกรรมก็มีข้อกำหนดการใช้งาน รวมถึงตัวแปรต้นและตัวแปรตามที่แตกต่างกัน จึงทำให้โพรโทคอลของ Fieldbus มีจำนวนมากและหลากหลาย แต่โพรโทคอลที่สามารถใช้งานได้ต่อเนื่องยังปัจจุบันจะขึ้นอยู่กับปัจจัยสำคัญอันหนึ่งกล่าวคือ โพรโทคอลนั้นจะต้องมีคุณสมบัติแบบเปิดและมีมาตรฐาน (open and standard) ซึ่งหมายถึงเป็นโพรโทคอลที่เปิดเผยข้อมูลแก่สาธารณะเพื่อให้โอกาศบริษัทผู้ผลิตต่าง ๆ สามารถเข้าถึงและใช้โพรโทคอลในอุปกรณ์ที่บริษัทนั้น ๆ ผลิตได้ ไม่ใช่เป็นสมบัติเอกสิทธิ์เฉพาะสำหรับบริษัทหนึ่งบริษัทใดที่ปกปิดและห้ามใช้ทั่วไป และมีมาตรฐานรองรับที่อุปกรณ์ที่ผลิตจากหลากหลายบริษัทสามารถทำงานร่วมกันได้ อันนำไปสู่ความน่าเชื่อถือของผู้บริโภคที่จะเลือกใช้โพรโทคอลนั้นและลงทุนซื้อเครื่องจักรในกระบวนการผลิตที่รองรับโพรโทคอลที่มีความน่าเชื่อถือต่อไป และเป็นสูตรสำเร็จที่ทำให้บริษัทผู้ผลิตเครื่องจักรเลือกใช้โพรโทคอลที่ได้รับการยอมรับต่อเนื่องและยืนยาว
นักพัฒนาโพรโทคอลของระบบ Fieldbus ได้พัฒนาตามแนวทางรูปแบบ OSI โดยอาศัยโพรโทคอล Medium Access Control (MAC) ในชั้น data link ในการสื่อสารโดยอาศัยเทคนิค time division multiple access (TDMA) ซึ่ง bandwidth จะถูกใช้ร่วมกันใน time domain เป็นหลัก และการสื่อสารด้วยเทคนิคอื่นกล่าวคือ Frequency Division Multiple Access (FDMA), Code Division Multiple Access (CDMA) และ Space Division Multiple Access (SDMA) ไม่ได้ถูกใช้งานในระบบ Fieldbus
ตัวอย่างของโพรโทคอลในระบบ Fieldbus [4] ที่ใช้วิธีการสื่อสารที่ต่างกัน มีบางโพรโทคอลที่ยังได้รับความสนใจจากผู้ใช้งานในปัจจุบัน เช่น PROFIBUS (Process Field Bus) ซึ่งแนะนำเข้าสู่อุตสาหกรรมจาก BMBF (German department of education and research) และต่อมาใช้โดยบริษัท Siemens , Modbus RTU ซึ่งแนะนำเข้าสู่อุตสาหกรรมจากบริษัท Modicon และต่อมาใช้โดยบริษัท Schneider Electric, CAN (Controller Area Network) ซึ่งแนะนำมาจากอุตสาหกรรมรถยนต์ โดยบริษัท Bosch GmbH และมีการใช้โพรโทคอลอื่น ๆ ซึ่งอาศัยการสร้างชั้น application อยู่บน CAN เช่น DeviceNet, CANopen และ SDS เป็นต้น
ข้อเด่นของระบบ Fieldbus ได้แก่ โพรโทคอลที่เป็นแบบ deterministic ซึ่งสามารถคาดการณ์เหตุการณ์ในอนาคตได้จากข้อมูลปัจจุบันและอดีต มีการสื่อสารแบบ real time มีความทันเวลา (timeliness) และ มีความเชื่อมั่นของสัญญาณ (reliability)
2) Industrial Ethernet
ระบบสื่อสารในโครงข่ายคอมพิวเตอร์ส่วนบุคคล อาศัยเทคโนโลยี Ethernet ซึ่งปัจจุบันได้พัฒนาให้ทันสมัยมาก ในแง่การรับส่งข้อมูล มีความสามารถในการรับส่งข้อมูลได้เร็วมากในช่วง Gigabit ต่อวินาที ตลอดจนความสามารถของ Application Specific IC (ASIC) ในการประมวลผลได้เพิ่มขึ้น รวดเร็วขึ้น และ มีขนาดเล็กลง ทำให้ติดตั้งลงในอุปกรณ์เคลื่อนที่ไร้สายได้ นอกจากนี้ราคาของอุปกรณ์ในระบบ Ethernet ก็ถูกลงมากสามารถพบเห็นในอุปกรณ์อิเล็กทรอนิกส์ทั่วไป เมื่อเปรียบเทียบการสื่อสารระหว่าง Ethernet กับ Fieldbus จะเห็นได้ว่ามีความแตกต่างกันในด้านประสิทธิภาพเป็นอย่างมาก จึงมีผลให้มีความต้องการ ใช้การสื่อสารแบบ Ethernet เข้าแทนที่การสื่อสารแบบ Fieldbus ในปัจจุบันมากขึ้นเรื่อย ๆ
ในขณะเดียวกัน ระบบอัตโนมัติมีความต้องการที่ซับซ้อนขึ้น ทำให้จำนวนตัวแปรต้นและตัวแปรตามเพิ่มขึ้นมาก นอกจากนี้ความต้องการใช้งานเกี่ยวกับภาพและเสียงในระบบอัตโนมัติอุตสาหกรรมเพื่อเพิ่มประสิทธิภาพของระบบ ทำให้ระบบ Fieldbus แบบเดิมไม่สามารถรองรับความต้องการในการสื่อสารข้อมูลที่เพิ่มมากขึ้นได้
โดยพื้นฐานแล้วการสื่อสารแบบ Ethernet ไม่สามารถประยุกต์ใช้โดยตรงบนระบบอัตโนมัติอุตสาหกรรม เนื่องจาก Ethernet เป็นการสื่อสารแบบ nondeterministic ทำให้ต้องพัฒนาโพรโทคอลใหม่ที่มีความสามารถนี้ และสามารถควบคุมในเวลาจริง (Real time control) ได้
โพรโทคอลสำหรับ Industrial Ethernet ได้แก่ EtherNet/IP, PROFINET, EtherCAT, Modbus TCP, POWERLINK, SERCOS III และ CC-Link IE โดยมีรายละเอียดในตารางที่ 1
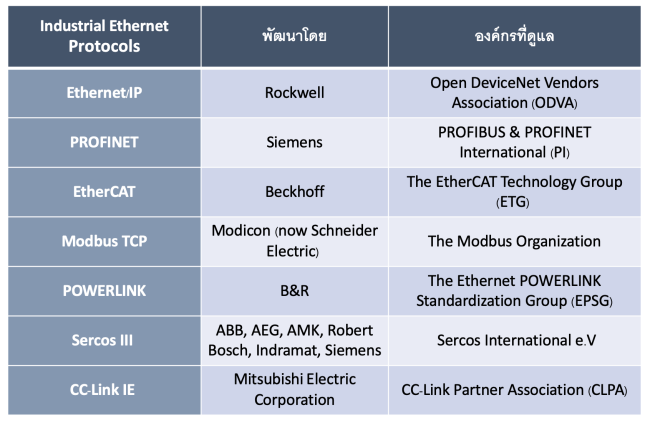
ในส่วนของอุปกรณ์ที่เกี่ยวข้องกับ Industrial Ethernet นั้นประกอบด้วย hardware เช่น Ethernet hub, Ethernet switches, Routers และสายเคเบิล เป็นต้น และ software solution โดยมีบริษัทผู้เล่นรายใหญ่ต่าง ๆ ที่มีสินค้าและบริการ ดังรายนามต่อไปนี้ Siemens, Schneider Electric, Rockwell Automation, Beckhoff Automation, Cisco, Belden, B&R Automation, Eaton, Endress+Hauser, Parker Hannifin, ABB, Bosch Rexroth, GE, Honeywell International, IDEC, Hitachi, OMRON, ACS Motion Control Ltd.
นอกจากนี้ยังมีข้อมูลการวิจัยตลาดเกี่ยวกับ Industrial Ethernet โดยต้องเสียค่าสมาชิกในการเข้าถึงข้อมูลเช่น https://www.marketresearchfuture.com/reports/industrial-ethernet-market-4829 เป็นต้น
การเปรียบเทียบโพรโทคอล Industrial Ethernet สำหรับ PLC
ในเอกสารซึ่งเผยแพร่ใน www.ethercat.org ได้นำเสนอเอกสารเปรียบเทียบโพรโทคอล Industrial Ethernet ได้แก่ EtherCAT, EtherNet/IP, Powerlink, PROFINET IRT (Isochronous Real-Time) และ SERCOSIII โดยแบ่งลักษณะของโพรโทคอลออกเป็น 3 ประเภทได้แก่
- 1) ชนิด Standard Software และ Standard Ethernet
- เป็นโพรโทคอลที่อาศัยลำดับชั้นของTCP/IP และมีกลไกการทำงานเวลาจริงบนชั้นสูงสุด การใช้เทคนิคนี้จะให้ประสิทธิการสื่อสารอยู่ในช่วงที่จำกัด โพรโทคอลที่ใช้เทคนิคนี้ได้แก่ Ethernet/IP
- 2) ชนิด Open Software และ Standard Ethernet
- เป็นโพรโทคอลที่มีชั้นสร้างใหม่อยู่บนชั้นของ Ethernet เดิม และมีการสร้างการควบคุมโดยซอฟต์แวร์ที่เป็นกรรมสิทธิ์ในชั้น 3 และ 4 ในแบบจำลอง OSI เพื่อทำให้การจัดการลำดับเวลาในการสื่อสารเป็นแบบ determinism โพรโทคอลที่ใช้เทคนิคนี้ได้แก่ Powerlink
- 3) ชนิด Open Software และ Modified Ethernet
- เทคนิคนี้อาศัยการสร้างมาตรฐานใหม่และยังคงใช้อุปกรณ์เดิมของ Ethernet แต่มีการเพิ่มเติมด้วยการสร้างซอฟต์แวร์ใหม่ที่เปิดเผยต่อสาธารณะและมีการเพิ่มเติมอุปกรณ์การตัดต่อพิเศษ (Special switch) หรือชิป ASIC ติดตั้งบนอุปกรณ์สื่อสาร โพรโทคอลที่ใช้เทคนิคนี้ได้แก่ EtherCAT, PROFINET IRT และ SERCOS III
ในการประยุกต์ใช้ Industrial Ethernet สามารถแยกความต้องการการใช้งานออกเป็น 3 กลุ่ม ได้แก่
- ก) กลุ่มต้องการความเร็วต่ำโดยมีความต้องการเวลาในการตอบสนองในช่วง 100 ms ซึ่งกลุ่มนี้มีลักษณะให้มนุษย์มีส่วนร่วมในการสังเกตุการณ์ เช่น การตรวจสอบกระบวนการ โดยส่วนมากระบบอัตโนมัติควบคุมการผลิตและระบบควบคุมอาคารจะอยู่ในกลุ่มนี้
- ข) กลุ่มต้องการความเร็วปานกลางโดยมีความต้องการเวลาในการตอบสนองน้อยสุดต่ำกว่า 10 ms ซึ่งเป็นกลุ่มงานการควบคุมเครื่องจักรด้วย PLC
- ค) กลุ่มต้องการความเร็วสูงโดยมีความต้องการเวลาในการตอบสนองต่ำกว่า 1 ms ซึ่งเป็นกลุ่มงานเกี่ยวข้องกับการควบคุมการเคลื่อนไหวหรือหุ่นยนต์
ความสามารถของโพรโทคอลทั้ง 5 พบว่า เวลาในการตอบสนองมีค่า เท่ากับ หรือ น้อยกว่า 1 ms และแต่ละองค์กรที่ควบคุมดูแลโพรโทคอลแต่ละชนิดก็จะประชาสัมพันธ์เกี่ยวกับจุดเด่นของประโตคอลที่ตัวเองดูแล และมักจะมีข้อมูลแสดงผลว่า โพรโทคอลของตัวเองมีเวลาในการตอบสนองมีค่าน้อยที่สุด เมื่อเทียบกับโพรโทคอลอื่น ๆ ดังนั้นการพิจารณาเอกสารจากแหล่งข้อมูลใด ๆ ที่อ้างว่า เป็นโพรโทคอลที่มีเวลาในการตอบสนองมีค่าน้อยที่สุด [6,7] ซึ่งมีนัยยะว่าเป็นโพรโทคอลที่ดีที่สุด จึงต้องทำการวิเคราะห์อย่างระมัดระวังในเรื่องกระบวนการทดสอบที่ใช้เทคนิคแตกต่างกัน เพราะการประชาสัมพันธ์ว่าเป็นโพรโทคอลที่ดีที่สุดจะเล็งเห็นผลให้เกิดผลประโยชน์ทางธุรกิจมหาศาลเกิดขึ้นกับองค์กรที่ควบคุมดูแลโพรโทคอลนั้น ๆ
การวิเคราะห์และสรุปผล
เนื่องจากประเทศไทยไม่ได้ผลิตเทคโนโลยีเกี่ยวกับ Industrial Communications เอง ดังนั้นองค์กรภาครัฐและบริษัทเอกขนจึงต้องให้ความสำคัญในการประเมินเทคโนโลยีที่จะใช้ในแง่ของประสิทธิภาพต่อราคาเสมอ จากข้อมูลทางเทคนิคจะเห็นได้ว่า เทคโนโลยีการสื่อสาร Industrial Ethernet จะมีความสำคัญเพิ่มมากขึ้นในระบบอัตโนมัติอุตสาหกรรม โดยจะเป็นเทคโนโลยีการสื่อสารที่บริษัทผู้ผลิตเครื่องจักรใหม่เลือกใช้แทนที่ระบบ Fieldbus เดิม แต่การใช้เทคโนโลยี Industrial Ethernet ยังไม่สามารถแทนที่ระบบ Fieldbus ได้ทั้งหมดในเวลาอันใกล้นี้ เนื่องจากสายการผลิตที่ใช้งานเครื่องจักรเก่ายังมีการใช้งานอยู่มาก ดังนั้นการพัฒนาปรับปรุงสายการผลิตเก่าเป็นแบบใหม่จึงเป็นเหตุปัจจัยที่แต่ละองค์กรหรือบริษัทจะต้องทำการตัดสินใจทางธุรกิจเพื่อให้คุ้มค่ากับการลงทุน
ดาวน์โหลดเอกสารเผยแพร่

เอกสารอ้างอิง
- S. Vitturi, P. Pedreiras, J. Proenza, and T. Sauter, “Guest Editorial Special Section on Communication in Automation,” IEEE Transactions on Industrial Informatics, vol. 12, no. 5, pp. 1817–1821, 2016.
- B.M. WIlamowski and J.D. Irwin, Eds., The Industrial Electronics Handbook, Second Edition, Industrial Communication System. Boca Raton, FL: CRC Press, Taylor & Francis Group, 2011.
- T. Sauter, “The three generations of Field-level networks – Evolution and compatibility issues,” IEEE Trans. Ind. Electron., vol. 57, no. 11, pp. 3585-3595, Nov. 2010.
- T. Sauter, “Fieldbus System Fundamentals,” in Industrial Communication Technology Handbook, 2nd ed., R. Zurawski, Ed., Boca Raton, FL: CRC Press, Taylor & Francis Group, 2015, pp. 1-50.
- ISA-95.00.01-CDV3 Enterprise-Control System Integration Part 1, Available: http://citeseerx.ist.psu.edu/viewdoc/download?doi=10.1.1.460.8814&rep=rep1&type=pdf
- “The Best Ethernet Protocol For Your PLC: 5 Fieldbuses Compared For Industry 4.0,” Kingstar, 2017, Available: https://www.automation.com/pdf_articles/kingstar/Best_Ethernet_Protocol_for_Your_PLC.pdf
- “Industrial Ethernet Facts, System Comparison The 5 Major Technologies,” 2nd ed., 2013, Available: https://www.ethernet-powerlink.org/fileadmin/user_upload/Dokumente/Downloads/Industrial_Ethernet_Facts/EPSG_IEF2ndEdition_en_WEB_01__3_.pdf